

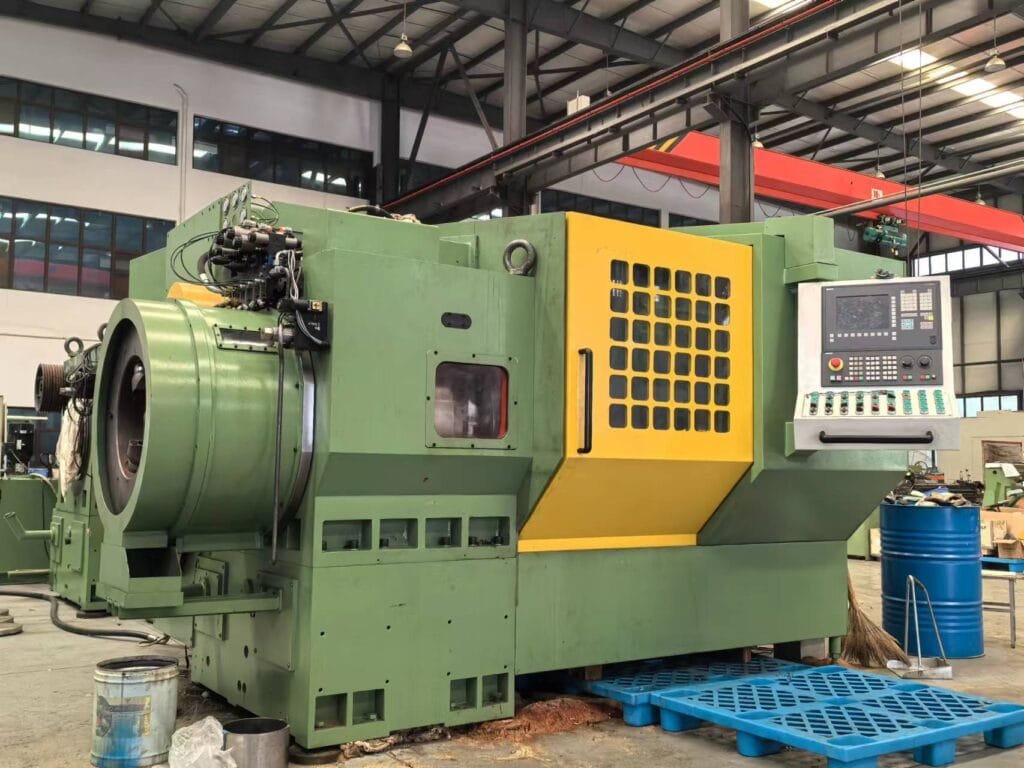
Specification of the CNC Pipe Threading Machine
Item | Unit | DSMT-5 | DSMT-7 | DSMT-13 | DSMT-20 |
---|---|---|---|---|---|
Performance | |||||
Processed Tube Dia | mm | 1.9″-4 1/2″ | 2 3/8″-7′ | 4 1/2“-13 3/8” | 9 5/8“ -20” |
Processed Tube Length | mm | 4620mm-12500 mm | 4620mm-12500 mm | 4620mm-12500 mm | 4620mm-12500 mm |
Spindle System | |||||
Spindle Through Hole Dia | mm | 145 | 165 | 380 | 640 |
Spindle Speed | Rpm | 300-1000 | 150-1000 | 50-400 | 50-400 |
Spindle Motor | kw | 110 | 160 | 160 | 190 |
Height of spindle center from ground | mm | 1200 | 1200 | 1200 | 1290 |
Feeding System | |||||
X1/Y1/Z1 axis Travel | mm | 110/110/550 | 110/110/550 | 160/160/550 | 400/600 |
X2/Z2 Axis Travel | mm | 140/700 | 140/700 | 140/700 | / |
X1/Y1/Z1 axis Fast Speed | m/min | 15 | 15 | 15 | 15 |
X2/Z2 Axis Fast Speed | m/min | 20 | 20 | 20 | / |
Hydraulic Turret | |||||
Positions | Station | 5-6 | 5-6 | 5-6 | 5-6 |
Drive Pattern | Servo motor or hydraulic motor drive rotation | Servo motor or hydraulic motor drive rotation | Servo motor or hydraulic motor drive rotation | Servo motor or hydraulic motor drive rotation | |
Hydraulic System | |||||
Hydraulic Pump Motor | kw | 5.5kw | 5.5kw | 5.5kw | 5.5kw |
Pump Flow | L/Min | 40 | 40 | 40 | 40 |
Machine Work Pressure | Bar | 70 | 70 | 70 | 70 |
Hydraulic Oil tank Capacity | L | 200 | 200 | 200 | 200 |
Accumulator capacity | l | 20 L ( 35bar ) | 20 L ( 35bar ) | 20 L ( 35bar ) | 20 L ( 35bar ) |
Spindle Cooling and Lubricating System | |||||
Oil Pump Motor Power | HP | 3 | 3 | 3 | 3 |
Oil Pump Flow | L/Min | 60 | 60 | 60 | 60 |
Working Pressure | Bar | 3-5 Bar | 3-5 Bar | 3-5 Bar | 3-5 Bar |
Oil Tank Capacity | L | 160 L | 160 L | 160 L | 160 L |
Centralized Lubricating System | |||||
Oil Pump Motor Power | W | 20 | 20 | 20 | 20 |
Oil Pump Flow | L/min | 0.15L /Min | 0.15L /Min | 0.15L /Min | 0.15L /Min |
Working Pressure | Bar | 20 | 20 | 20 | 20 |
Oil Tank Capacity | L | 4l | 4l | 4l | 4l |
Emulsion cooling system | |||||
Emulsion Pump Motor | Kw | 4 | 4 | 4 | 4 |
Emulsion Pump Flow | L /Min | 100 | 100 | 100 | 100 |
Working Pressure | Bar | 25 | 25 | 25 | 25 |
Water Tank Capacity | L | 1200 | 1200 | 1200 | 1200 |
Working Accuracy | |||||
Position Accuracy (x/y/z) | mm | 0.012 / 0.012 /0.020 | 0.012 / 0.012 /0.020 | 0.012 / 0.012 /0.020 | 0.012 / 0.012 /0.020 |
Repeated Position Accuracy (X/Y/Z ) | mm | 0.008 / 0.008 /0.010 | 0.008 / 0.008 /0.010 | 0.008 / 0.008 /0.010 | 0.008 / 0.008 /0.010 |
Backlash (X1/Y1/Z1) | mm | 0.02 | 0.02 | 0.02 | 0.02 |
Workpiece circular run-out error | mm | +- 0.01 mm /200mm | +- 0.01 mm /200mm | +- 0.01 mm /200mm | +- 0.01 mm /200mm |
Surface roughness of workpiece | Not Less Than Ra1.6 | Not Less Than Ra1.6 | Not Less Than Ra1.6 | Not Less Than Ra1.6 | |
Control System | |||||
NC System | Siemens 840 Ds1 | Siemens 840 Ds1 | Siemens 840 Ds1 | Siemens 840 Ds1 |
The Main Parts of the CNC Pipe Threading Machine
01.
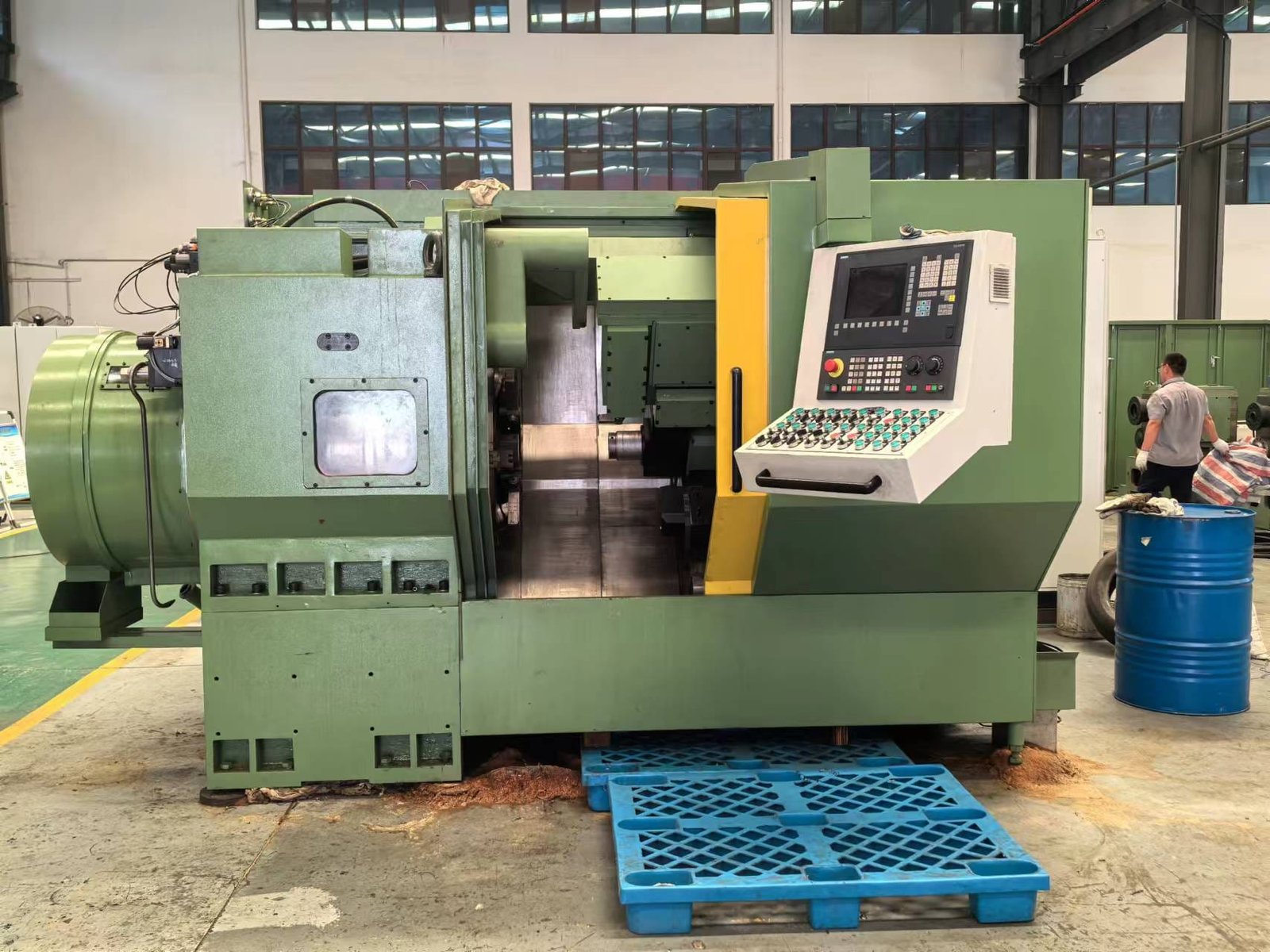
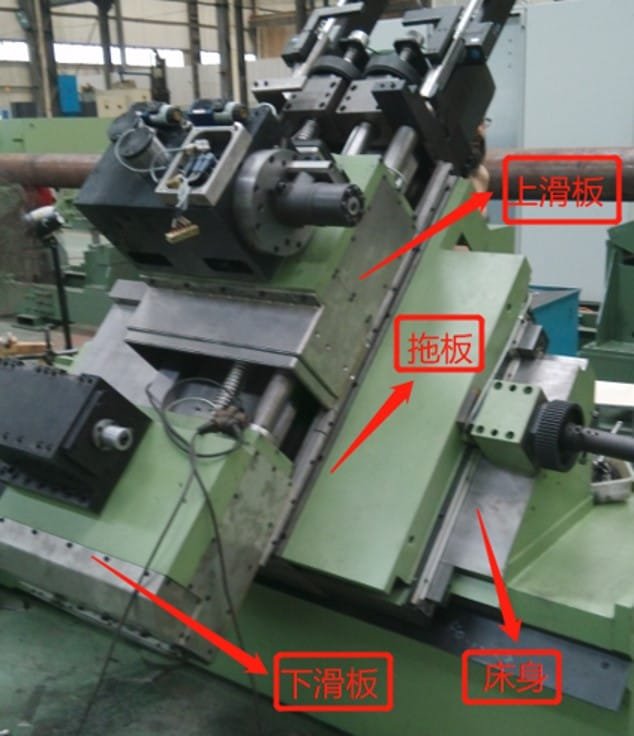
02.
03.


04.
05.

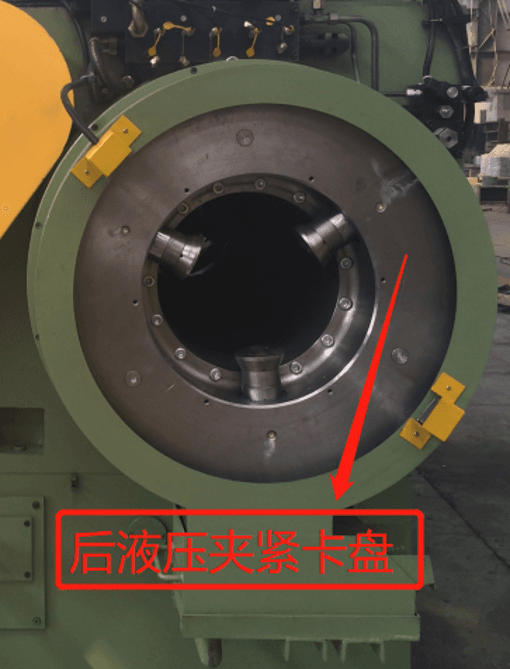

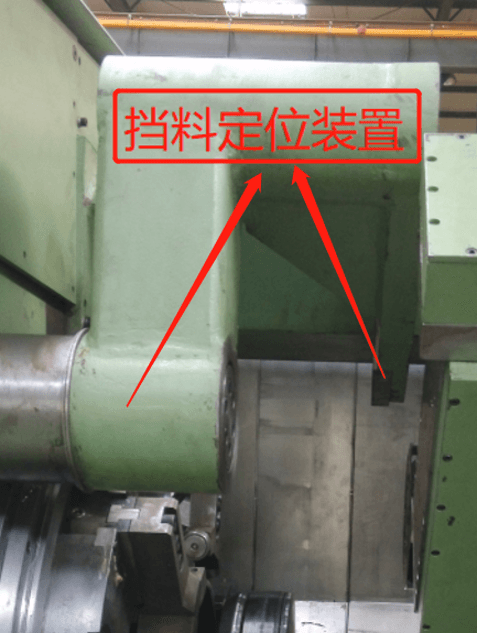
06.
07


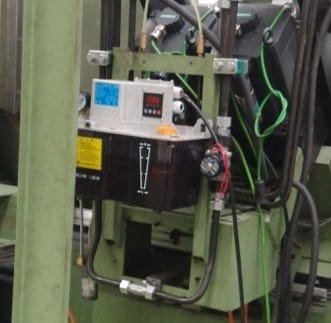

08.
The lubrication system of the spindle unit extracts the lubricating oil in the bed oil tank of the motor oil pump group to forcibly lubricate the bearing, gear and other lubricating points in the spindle box and play a cooling role, which is a pressure injection lubrication cycle. Filters and electronic flow switches are configured to monitor the lubrication flow at relevant critical lubrication points and inform the operator whether the lubrication system is functioning properly
The auxiliary platform automatic lubrication system uses Perma or SKF (using electrochemical reaction principle) brand automatic lubrication system to achieve effective lubrication of each lubrication point.
09.
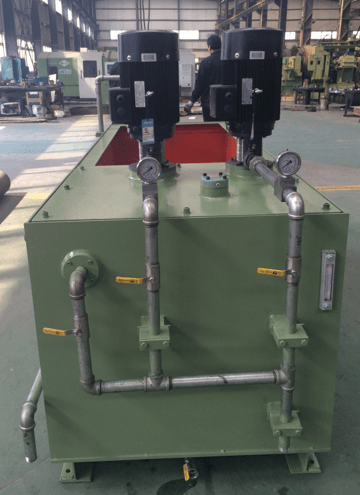

10.
09.
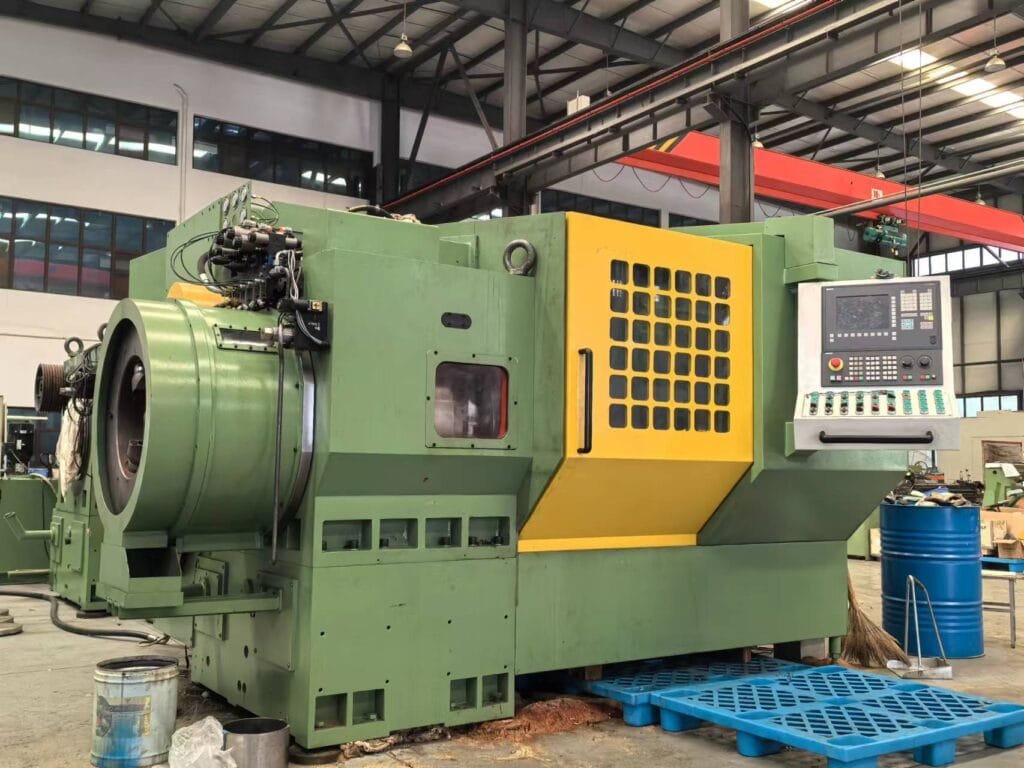
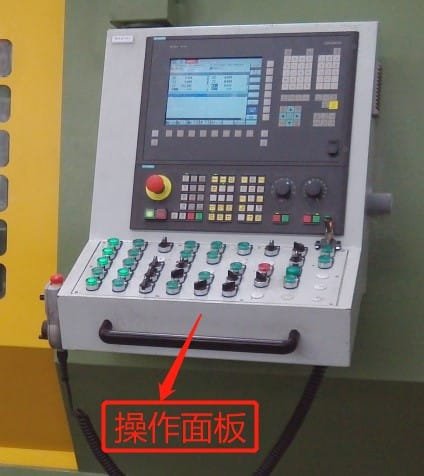
10.
Our Partner

