
Specification of the Pipe Cutting Machine
Item | Unit | DSQG-13 | DSQG-18 | DSQG-25 | DSQG-28 |
---|---|---|---|---|---|
Cutted Pipe Dia | Inch | 4 1/2 ”- 13 3/8 ” | 7 ”- 18 ” | 12 3/4 ”- 25 ” | 14 ”- 28” |
Max Pipe Wall Thickness | mm | 32 | 40 | 50 | 60 |
Max Process Pipe Length | mm | 6000-15000 | 6000-15000 | 6000-15000 | 6000-15000 |
Spindle Speed Range | rpm | 50-400 | 40-320 | 35-150 | 30-140 |
Feeding Stroke | mm | 50 | 75 | 90 | 100 |
Main Motor Power | Kw | 37 | 45 | 55 | 55 |
Cutting Accuracy | mm | 0.2 | 0.2 | 0.2 | 0.2 |
Machining pipe ends and pipes Perpendicularity of the axis | mm | 0.15/100 | 0.15/100 | 0.15/100 | 0.15/100 |
Machining surface roughness | um | Ra6.3 | Ra6.3 | Ra6.3 | Ra6.3 |
The Main Parts of the Pipe Cutting Machine
01.

1.2 The machine uses the gear differential feed principle to realize the longitudinal feed of the tool on the high-speed rotating cutter head to avoid machine vibration and extend the life of the pipe cutting tool. This ensures the Coupling faces roughness and verticality. The Machine adopts servo feed method and the structure has excellent stability, high repeated positioning accuracy and adjustable feed speed. The above structure can ensure the high efficiency and high quality of the pipe cutting machine.
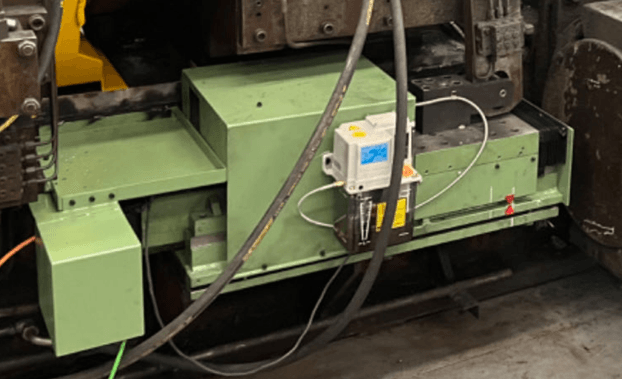
02.
03.
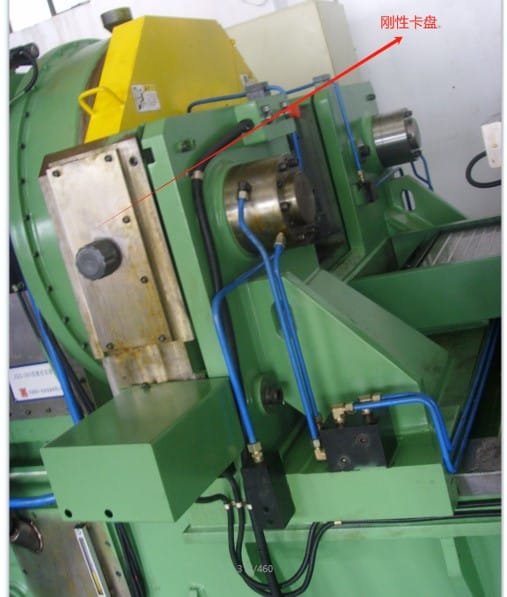
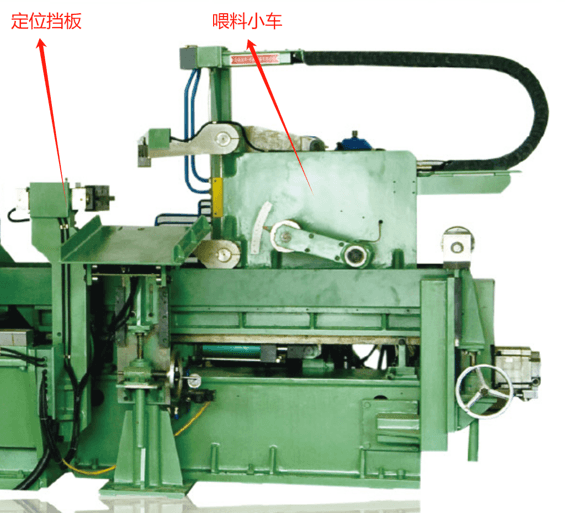
04.
04.
05.


06.
7.2 The lubrication system of the spindle unit adopts the motor oil pump group to extract lubricating oil from the bed oil tank to achieve forced lubrication and cooling of the bearing, gear, and other lubrication points in the spindle box, which belongs to the pressure injection lubrication method. The system is equipped with a filter and an electronic flow switch to monitor the lubrication flow at critical points, ensuring timely notification to the operator regarding information about lubrication system of the pipe cutting machine
7.3 Automatic lubrication system of auxiliary engine bench adopts manual lubrication to achieve effective lubrication of each lubrication point. Pipe cutting machine systems are equipped with liquid level alarm devices.
07.
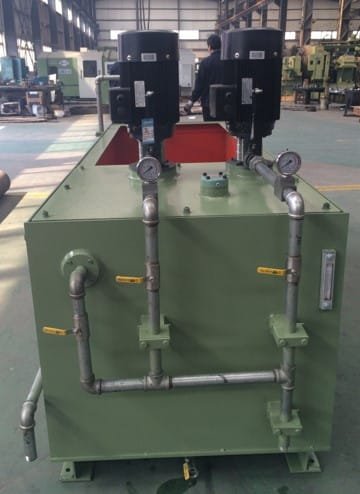
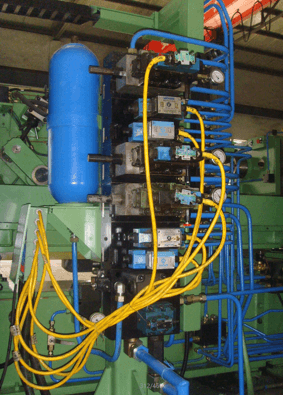
7.5 Hydraulic system: For the hydraulic pump station is completely independent so it can be installed according to the requirements of the end user. The device is mainly responsible for controlling all hydraulic actions of the machine main engine and the loading platform. The hydraulic valve stand installed at the headstock contains all solenoid valves, pressure reducing valves and other hydraulic actuators to control the clamping and centering of the hydraulic chuck claws, the stopper and the balance of the feed slide and the tool holder. Equipped with liquid level detection, pressure detection, and oil temperature detection devices, this makes the pipe cutting machine efficient and reliable.

08.
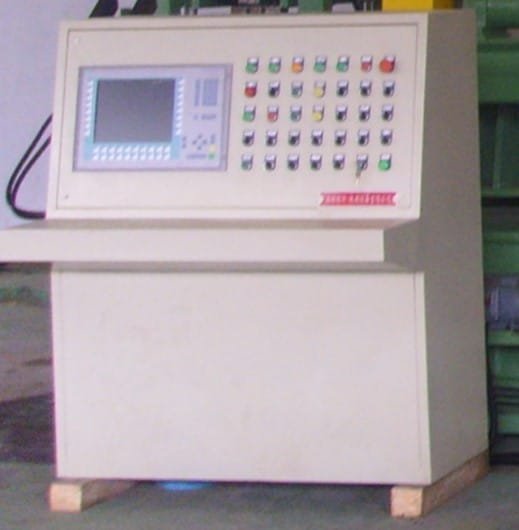
09-

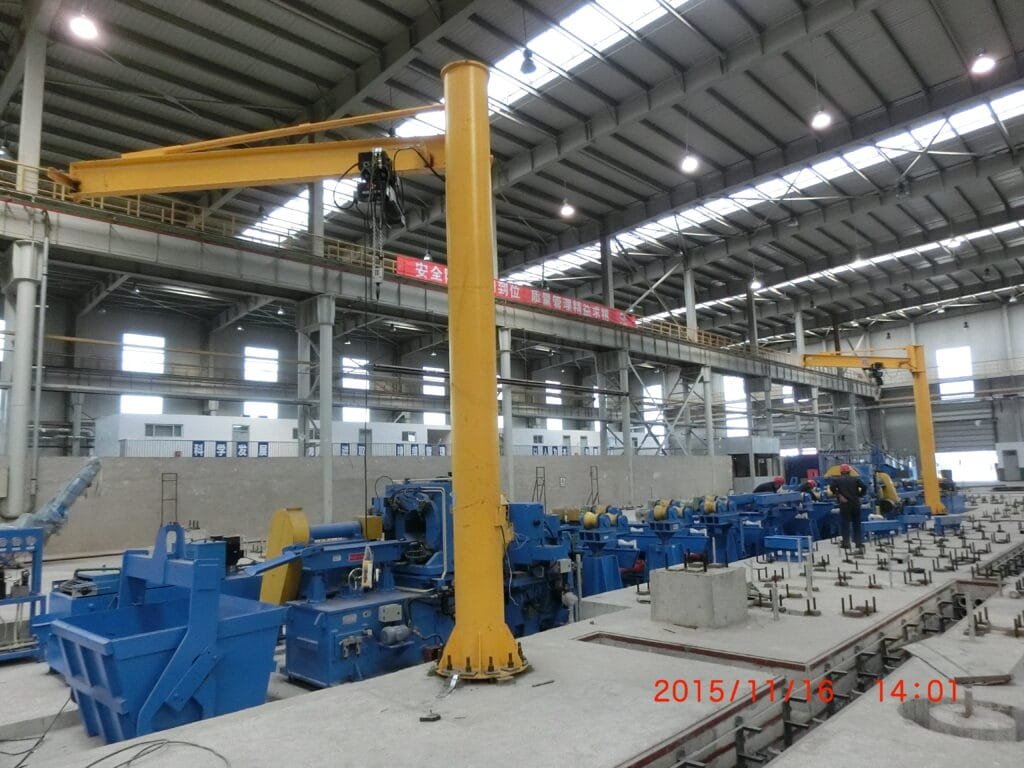
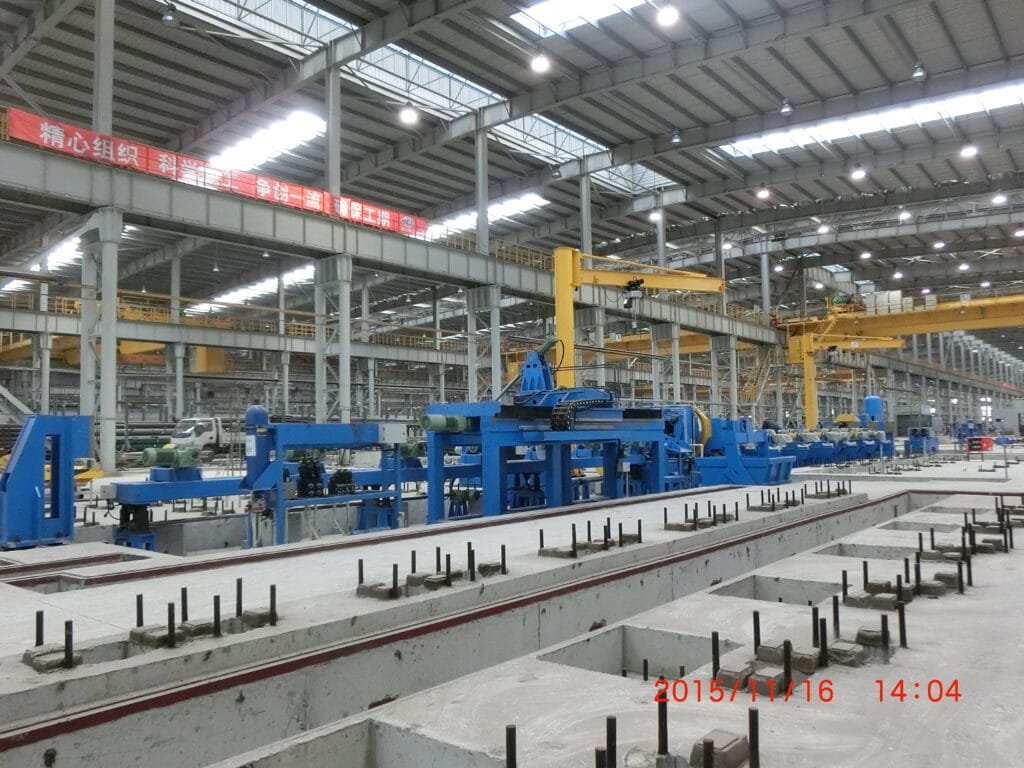

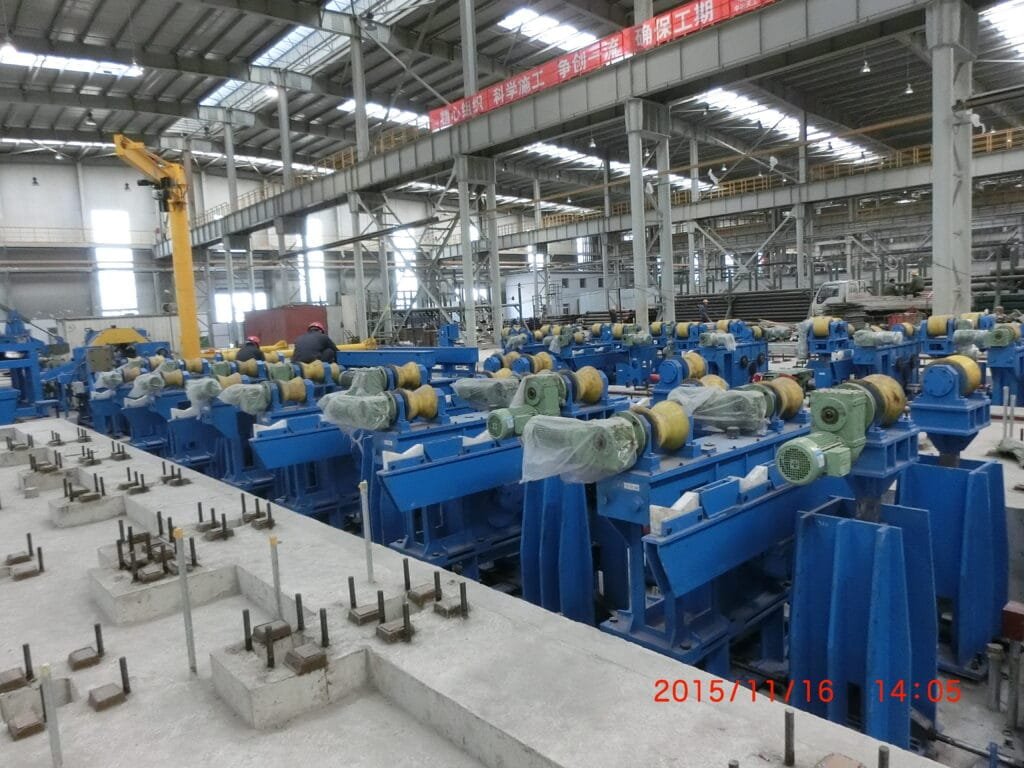
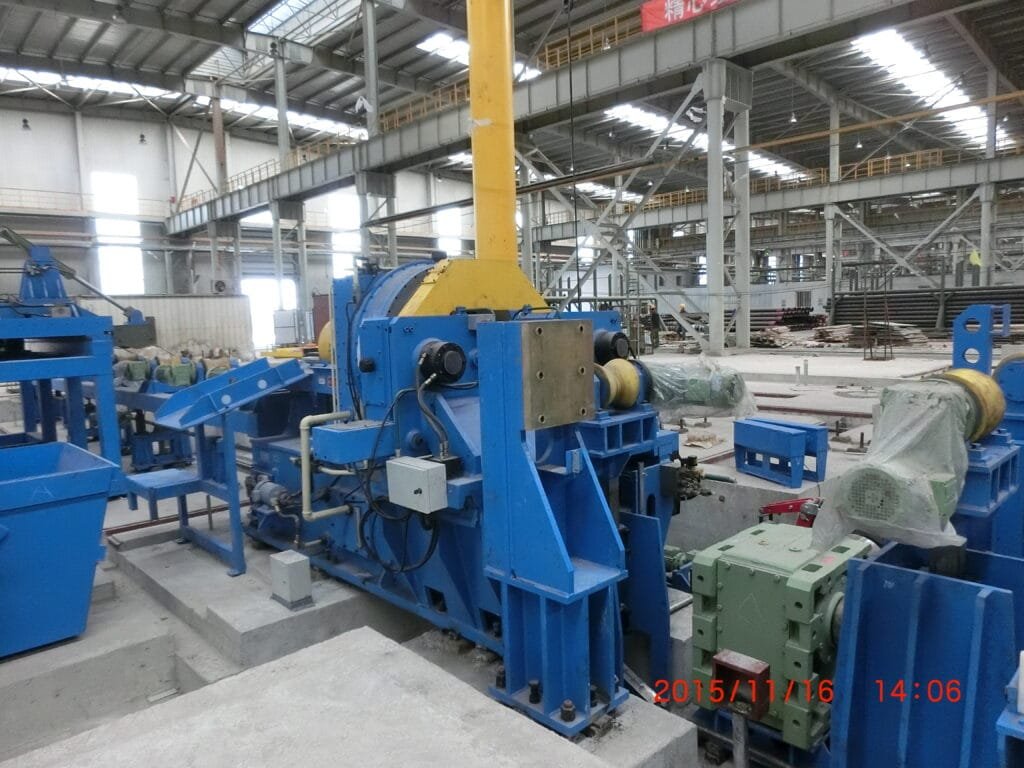
Our Partner

